In this project, a wing structure was imported into FEMAP and meticulously set up the wing mesh. I addressed any errors detected in the mesh using advanced techniques to guarantee high-quality results. Additionally, I harnessed post-processing tools to accurately analyze deformation and Von Mises stresses on the wing.
First, the wing structure model was imported into FEMAP, and its components were separated into layers for better organization. Then, each part was categorized under its corresponding element type by defining their properties. Skin, spars, and ribs were categorized as PLATE element types, while stringers, flanges, and trusses were categorized as ROD element types. Moreover, the material chosen for the entire structure was 6061 Aluminum. Finally, each part of the structure was meshed using the properties described in this paragraph. The following figures depict the final meshes for each part.
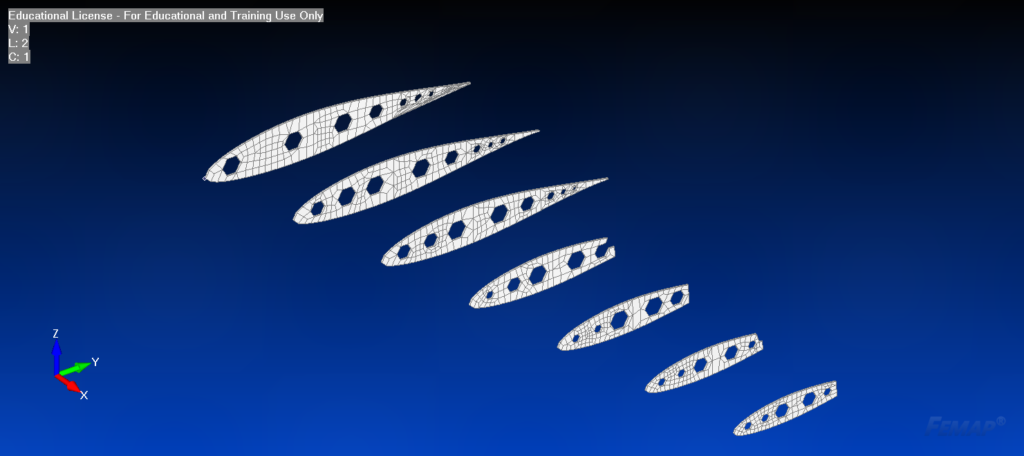
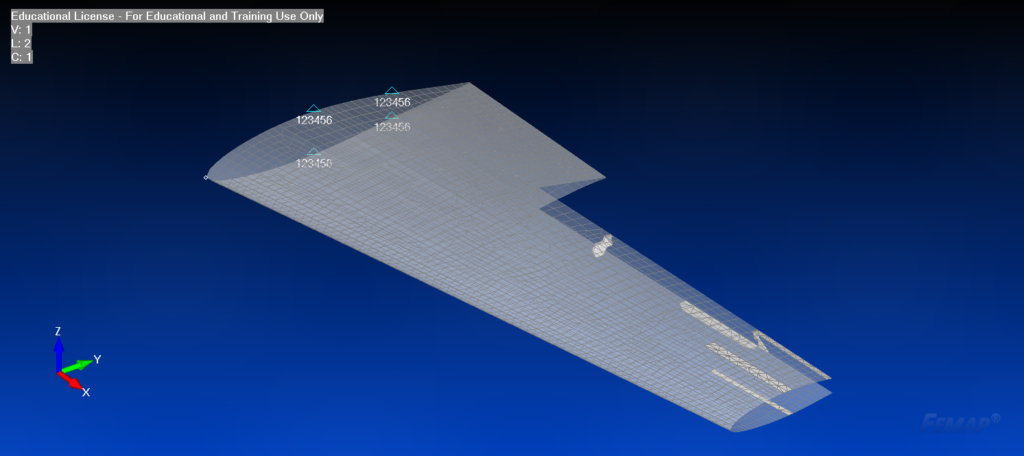
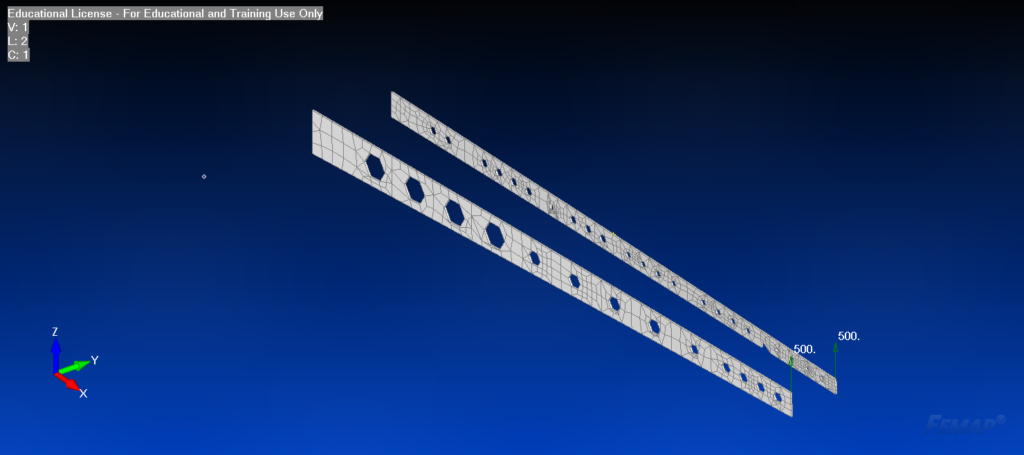
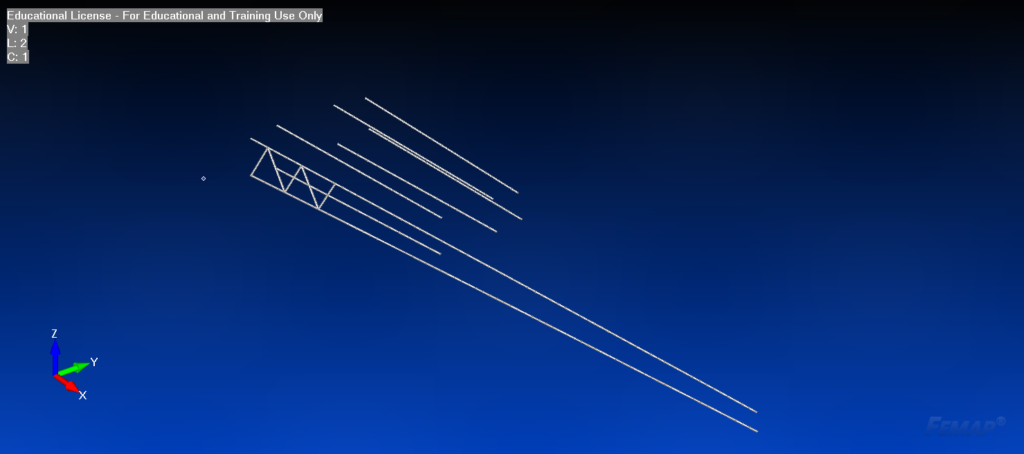
As can be seen from these figures, the skin mesh exhibits a few manual repairs due to disconnections within the entire mesh. Encountering such issues is a normal part of preparing a mesh for Finite Element Analysis (FEA). It’s crucial to address this problem to ensure the accuracy of the final analysis.
Mesh disconnections can be challenging to visualize. Therefore, it’s essential to utilize two helpful tools: Modal Analysis and View Free Edges. Both tools enable us to pinpoint any disconnections within the mesh. The following videos demonstrate how Modal Analysis results can be used to address this issue.
It is evident that a disconnection exists between the skin, ribs, and rear spar, particularly at the point where the aileron attaches to the wing structure. This issue has been resolved by eliminating unconnected nodes and elements, and manually creating new elements to ensure a seamless connection throughout the entire mesh. Subsequently, a second Modal Analysis was conducted to confirm the complete setup of the wing mesh. The following videos demonstrate that, following these necessary corrections, the mesh functions as a single, cohesive unit.
Once the mesh is corrected, it is possible to perform a Static Nodal Analysis to study the behavior of the wing structure. In this project, two Static Analyses with Nodal Forces and one Static Analysis with Pressure Forces were conducted.
For the Static Analysis with Nodal forces, the first one did not include the Stringers and Trusses in the analysis, while the second one did include the Stringers and Trusses. Both analyses provide a Contour Plot that displays the Von Mises stresses along the structure and the maximum displacement of the wing.
In both analyses, two forces of 500 pounds were applied to the tip of the wing, totaling 1000 pounds. The first analysis, which excluded Stringers and Trusses, can be viewed in video 6. The Total Translation for this analysis was 2.2834 inches.
The second analysis, this time incorporating Stringers and Trusses, is showcased in video 7. The total translation for this analysis amounted to 2.0922 inches.
From these two analyses, it can be appreciated that including stringers, flanges, and trusses can result in a stiffer wing structure, all without significantly increasing the weight of the structure.
Finally, the last static analysis with pressure forces was conducted to actually test our wing structure under forces similar to those caused by air flowing over a wing. In this analysis, pressure loads of 0.15 pounds per square inch were applied to the lower surface of the wing structure. These pressure loads do not equate to the nodal loads applied to the tip of the wing structures in the previous analysis. In fact, when a sum of forces is calculated, it can be appreciated that the wing has a total upward force of around 800 pounds, as opposed to the 1000 pounds applied in the previous analysis. Video 8 shows this analysis where the stringers, trusses, and flanges were not included. The total translation for this test was 0.531 inches.
In this project, a wing structure was imported into FEMAP and set up for Finite Element Analysis. These analyses allowed us to simulate how loads can affect the structure, resulting in a Von Mises contour plot and the total translation of the wing structure.
For future projects, instead of applying nodal forces or pressure forces directly to the wing structure, we could consider performing a Computational Fluid Dynamics analysis. This would enable us to obtain a function that describes the forces acting on the wing structure over time. We can then import this function into FEMAP, allowing for a more detailed description of how forces change over time in the Finite Element Analysis.