In this project, a radial engine with over 50 parts was modeled. Then it was performed kinematic simulations in the DMU Kinematics workbench to ensure proper engine functionality. Moreover, it was conducted finite element analysis using the Generative Structural Analysis workbench to guarantee that the engine and pistons can withstand combustion forces. Finally, an engine revision was performed to resolve over 200 clashes encountered during the design process.
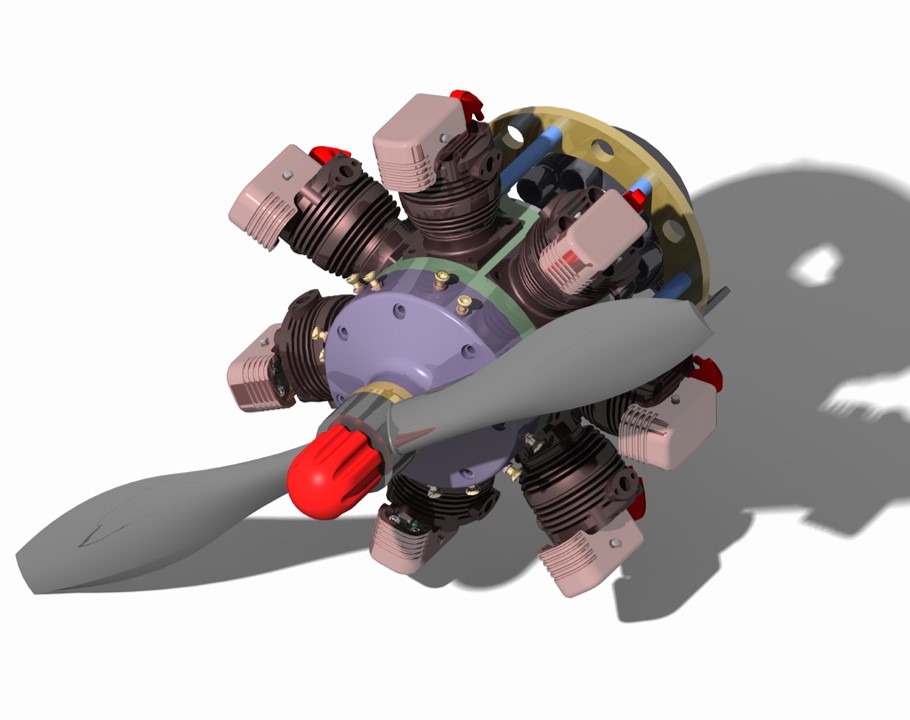
This was an advance project which had as main goal to use more workbenches that CATIA has to offer. The first workbench used in this project was the DMU kinematics, which has as main goal to analyze the behavior of a design under motion. For this project, it was tested the motion of the seven pistons in the engine. As a result, it was observed that some parts in the design crashed together and it did not behaved as expected. For these reasons, it was important to modify the classhing parts to ensure proper functionality of the pistons when they moved. Moreover, the DMU kinematics workbench was also used to measure the velocity and acceleration of a piston when moving.